Filter Press
A filter press is a widely-used piece of equipment in industrial filtration, separating liquids from solids. Plates are arranged parallel to each other with filter cloths or membranes installed on each surface. Slurry or sludge (liquid with suspended solids) enters the space between the plates. Positive pressure forces liquid through the cloth, compressing the solids into a cake with residual moisture. The cake is discharged by gravity when the plates are separated.
The main stages include feeding, compression, cake discharge, and cloth washing. Additional processes like secondary compression and air drying may be used depending on the materials and desired moisture content.
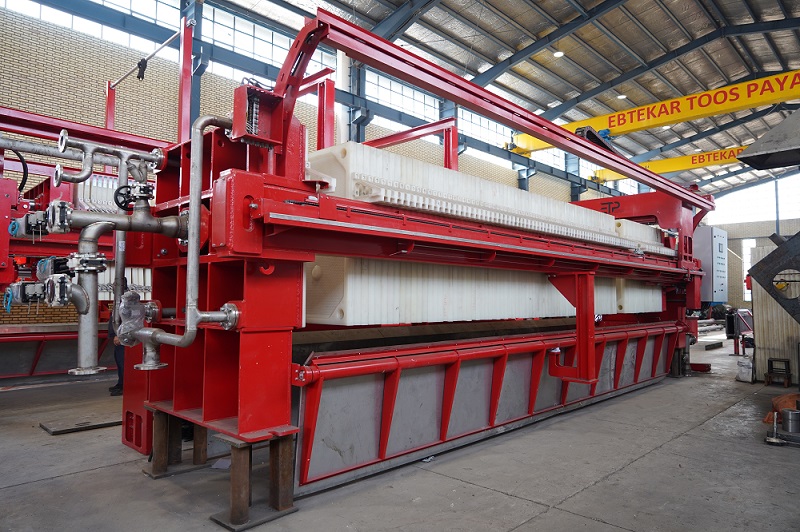
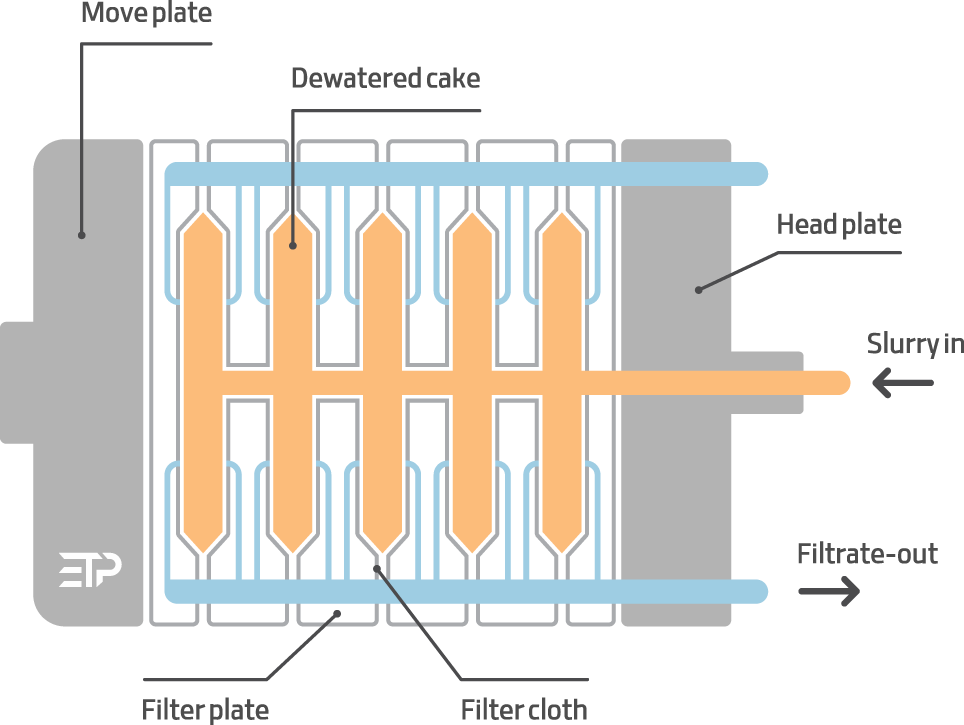
Overhead Filter Press
In the overhead filter press design, plates are suspended from a guide beam at the top of the machine and pressed by four hydraulic jacks. Full access to the plates for inspection and evaluation is a key feature.
General Features:
- High capacity for large filtration volumes
- No plate limitations; design flexibility for large-scale plates
- Quick plate opening and closing for shorter cycle times
- No plate movement required for cloth replacement
- Cloth vibrator option
- High- and low-pressure washing system options
- Good plate access for inspection and maintenance
- Lower force concentration and better body strength
- Reduced contamination of the plate handling system
Drawbacks:
Limited access to the plate handling system for repairs and servicing.
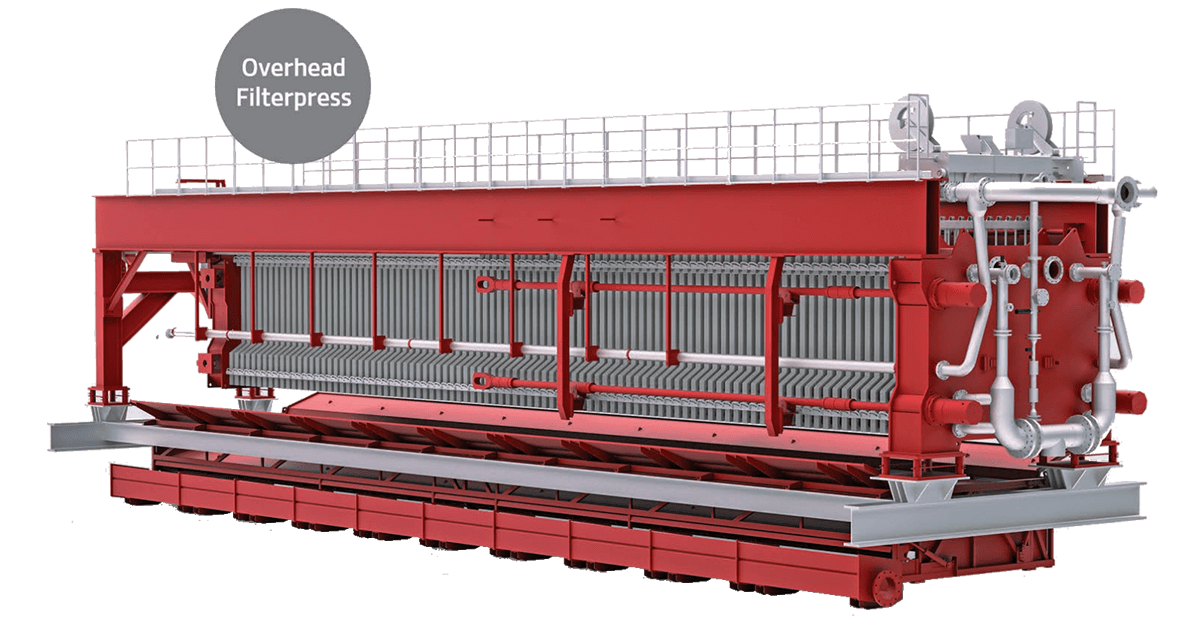
Large Plates
Structural Strength
High and LowPressure
Fast Operating
No Limit on The Plates
Sidebar Filter Press
In sidebar filter presses, plates are supported and slide on the sides of the machine using handles on rails embedded in the main body arms. The main body arms facilitate plate movement and act as tensile members to withstand pressure. Sidebar filter presses are available in trolley and robotic configurations, each tailored to specific industrial needs. This design diversity ensures optimal utilization in various processes.
Drawbacks:
- Increased force concentration at main arm junctions
- Plate shifting required for cloth replacement
- Limited plate access for inspection and cake discharge
- Potential contamination of plate shifting area
- Plate number limitations
General features:
- Simpler design
- Lower cost
- Variety in jack options
- Suitable for large and small sizes
- Improved access to plate shifting components
Some Limitations
Easy Repair
Simple Design
Low Cost
Features of Trolley Sidebar Filter Press
- Suitable for both product and waste
- Maximum plate size up to 2 meters
- Quick opening and closing of plates to reduce cycle time using the trolley mechanism
- Ability to install a cloth vibrator
- Capability to install both high-pressure and low-pressure washing systems for the plates.
High and Low Pressure
Large Plates
Fast Operating
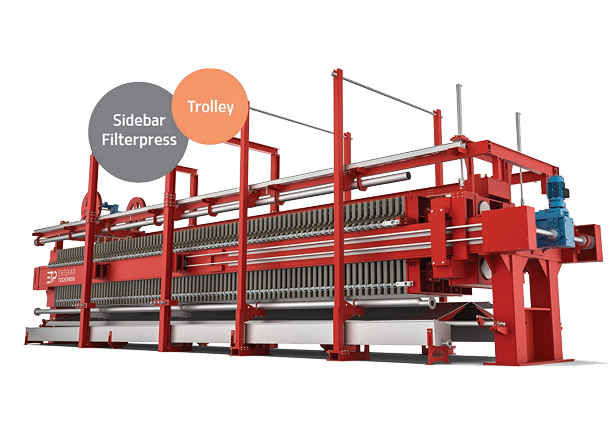
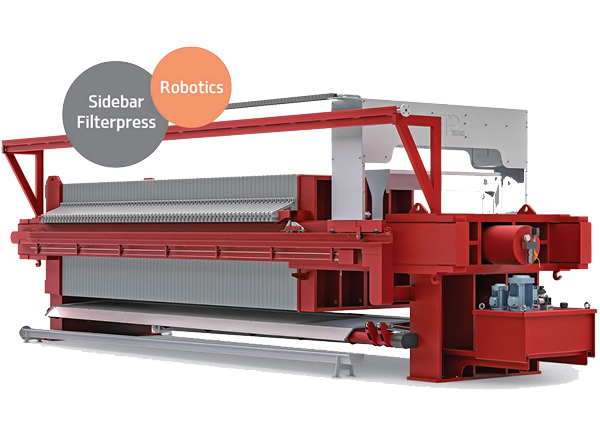
Features of the Robotic Sidebar Filter Press
- Lightweight and cost-effective structure
- Suitable for products and waste with a maximum plate size of up to 2 meters
- Capability to install a high-pressure plate washing system